Dry Granulation
The process, techniques and technologies.
Dry granulation is the most lean, efficient method for conditioning powders. Compared to wet granulation it uses less equipment and processing steps and is unlikely to damage the ingredients.
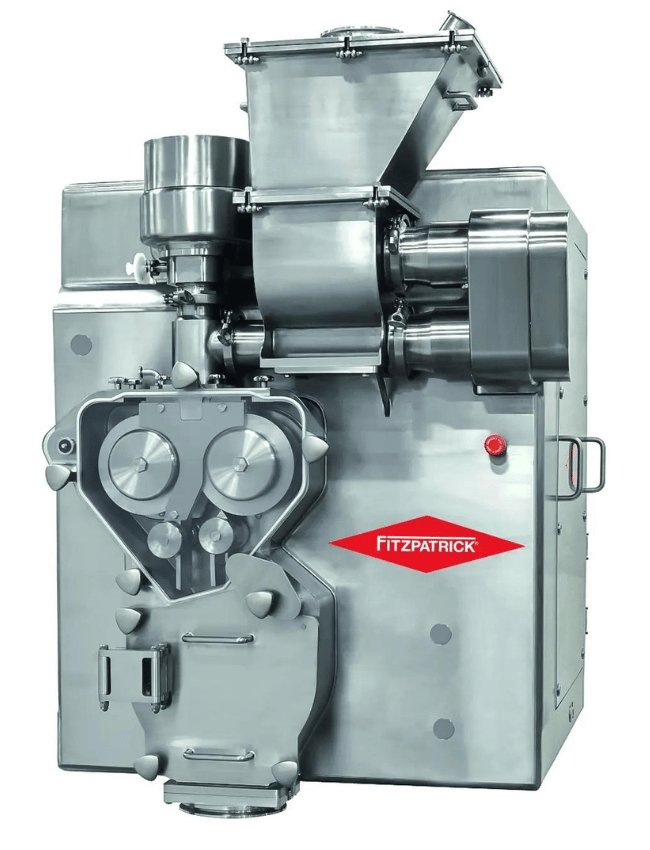
What is Dry Granulation?
Dry Granulation is a continuous manufacturing process that eliminates the need for additional time spent constructing batch sizes.
The process (sometimes referred to as pre-compression or double compression) compacts powders into larger pieces or rolls, that can be granulated (broken down) into a dosage form, often leading to a tablet manufacturing activity. With fewer process variables it is simpler to validate, optimize and scale. The dry granulation approach is a truly lean and straightforward way to condition powders.
Dry granulation is a well-established method that can help you to improve your processing versatility by enabling more efficient manufacturing.
With wet granulation, the batch size must match the machine's minimum and maximum fill capacities.
Dry Granulation Method
Dry Granulation using a Roll Compaction Machine is the process of compacting primary particles into larger granules in order to:
- Lock in blend ratios to prevent segregation later in the manufacturing process.
- Improve powder flow so that conveying and feeding into downstream processes is trouble-free, thereby eliminating caking and bridging.
- Condition powders prior to further downstream processing, i.e. enhancing compressibility for the tablet press stage.
- Control particle hardness and provide granule integrity during the conveying & processing steps.
- Create granular material that will dissolve or disperse in the most effective manner.
- Censify materials to reduce bulk density during storage, transport and packing.
- Control dust and reduce environmental risk, waste and cross-contamination.
/LCS-002web.png)
What is Dry Granulation?
Roll Compaction involves feeding powder between two counter-rotating rolls, where it is pressed together to create a dense, compact ribbon which is then milled to achieve a uniform particle size.
By controlling the following parameters on the Roll Compactor it is possible to generate the ideal powder for your process needs:
- Feed system design & speed
- Roll dimensions – diameter & width
- Roll speed, force & gap
- Roll surface profile
- Powder compact routing
- Mill rotor design & velocity
- Mill screen type & hole size
Learn more about our precise, clean and fast dry granulation machines.